Qu’est-ce que c’est ?
L’électro-érosion par enfonçage utilise une électrode sous tension, immergée dans un bain de diélectrique pour usiner des métaux conducteurs. Ce processus implique la création d’une électrode positive (généralement mâle) par rapport à la forme désirée que l’on souhaite obtenir dans l’usinage. Elle offre une méthode d’usinage efficace pour produire des pièces complexes difficiles à exécuter avec d’autres méthodes.
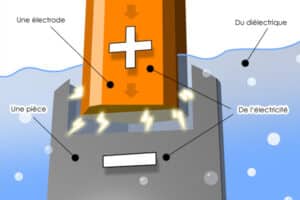
Au moment de l’enclenchement de la tension d’usinage, la broche déplace l’électrode-outil en direction de la pièce jusqu’au moment où l’électro érosion, c’est-à-dire le succession de décharges, peut s’effectuer. Le meilleur rendement est atteint lorsque l’électrode-outil maintient une position permettant d’assurer la continuité de ces décharges. Cette continuité ne peut se manifester que si l’électro-outil est pourvue d’un mouvement d’avance précis. Cette avance est fonction de facteurs nombreux et variables tels que :
Le régime choisi – la forme et la dimension de la surface – les conditions d’usinage et d’arrosage
Il serait évidemment très difficile de lier l’avance à tous ces facteurs sans avoir recours à l’automatisation qui seule, peut assurer un usinage continu. Ce mouvement automatique est réalisé en utilisant l’une des caractéristiques propres à l’usinage par électro érosion, en l’occurrence la relation qui existe entre la tension moyenne des décharges et la distance d’étincelage qui sépare l’électrode et la pièce usinée. C’est ainsi que toute variation de cette distance se traduit automatiquement par une modification de ladite tension.
Principales caractéristiques
Vitesse et précision : la distance entre l’électrode et al pièce étant de quelques centièmes de millimètre lorsque la première décharge éclate, cette dernière donne au servomécanisme (mécanisme automatique) l’ordre d’annuler l’avance de l’électrode. Le temps de réaction doit être très court pour éviter un court-circuit ou un contact mécanique entre l’électrode et la pièce.
Puissance mécanique absorbée par la broche : la puissance doit être suffisante pour supporter : le poids de l’électrode surtout lorsqu’elle est en acier et la poussée du diélectrique injecté à travers l’électrode.
Le circuit diélectrique
Il se compose de deux parties :
Un bac d’usinage destiné à immerger la zone de travail. Ce dernier est équipé de contrôleurs de température, de niveau, de trop-plein et d’un bloc distributeur de diélectrique.
Un groupe de filtration adapté à la taille de la machine et à la puissance du générateur.
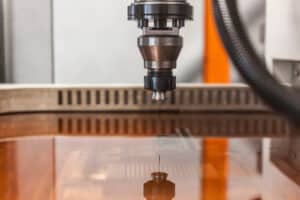
Le diélectrique
Son rôle est de concentré la décharge dans l’espace électrode-pièce et contribue ainsi à l’obtention de très fortes densités d’énergies nécessaires à l’enlèvement de la matière. Il entraîne les particules érodées et les produits de pyrolyse provoqués par la décharge hors intervalle d’usinage. Il contribue également au refroidissement de l’électrode et de la pièce au cours de l’usinage.
On rencontre sur le marché une grande diversité de liquides diélectriques. Actuellement deux familles de diélectrique sont principalement utilisées : l’eau déionisée et les hydrocarbures (huiles et pétroles). L’eau déionisée et déminéralisée est utilisée comme diélectrique que pour le micro-usinage.
Les huiles
Pour les huiles, celles les plus utilisées comme diélectrique sont les huiles minérales. Elles sont très pauvres en arômes et ne contiennent que peu ou pas d’additifs, elles donnent les meilleurs résultats.
La viscosité de l’huile est importante : une haute huile de haute viscosité ne convient pas pour des opérations de finition, car à ces régimes, les gaps sont très faibles et un liquide visqueux a de la peine à circuler entre l’électrode et la pièce. En revanche en ébauche, le rendement d’usinage est le meilleur avec une huile épaisse.
Le point éclair du diélectrique est tout aussi important : un liquide dont le point d’éclair est trop bas a tendance à se vaporiser facilement et à dégager une grande quantité de gaz gênant le déroulement de l’usinage.
Commande de programmation d’érosion planétaire
Incorporée à la tête de la broche ou à la table, cette commande permet une combinaison de l’érosion en plongée avec la broche et un déplacement des autres axes simultanés (mouvement planétaire). Une importante variété de cycles d’usinage peut être programmée et permet l’usinage de formes compliquées au moyen d’électrodes de formes simples. Les principaux cycles d’usinage sont :
L’usinage unidirectionnel : dans la direction de l’un des axes machine X, Y ou Z.
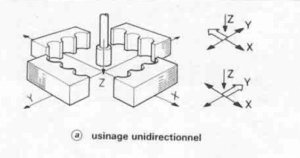
L’usinage orbital plan : il se fait dans le plan des deux axes simultanés X et Y. Il permet l’usinage de l’ébauche à la finition, avec la même électrode, de gravures de formes tridimensionnelles, la différence de gap étant compensée par le mouvement planétaire plan.
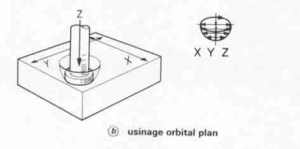
L’usinage orbital sphérique : il se fait dans les trois axes simultanés X, Y et Z. Il permet de maintenir une distance constante entre l’électrode et la pièce pour garantir, par exemple, l’épaisseur de tôle sur un outil d’emboutissage.
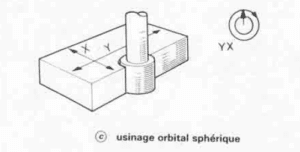
L’usinage conique : il se fait également dans les trois axes simultanés X, Y et Z. Il se fait également dans les trois axes simultanés X, Y et Z. Il permet l’usinage de dépouilles négatives ou positives rencontrées, par exemple, sur les outils de découpe.
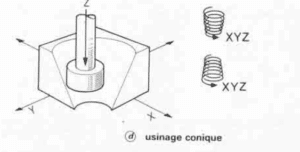
Les matériaux des électrodes
Les principaux matériaux d’électrodes utilisés sont les cuivres, le cupro tungstènes, les aciers et les graphites. Chez Micro Erosion, nous usinons nos propres électrodes en cuivre et en cupro tungstène.
Le cuivres
En enfonçage, le cuivre constitue 30 à 40 % des électrodes avec un comportement en usinage très satisfaisant.
Les électrodes en cuivre électrolytique sont réalisées principalement par extrusion, filage et étirage, électroformage, déformation à chaud ou à froid ou usinage traditionnel.
L’apport, à faible teneur (1 à 3%), de tellure, de Chrome ou de plomb dans le cuivre électrolytique améliore les qualités d’usinage par enlèvement de copeaux. Ces cuivres s’usinent avec presque autant de facilité que le laiton et, de ce fait, il est possible d’usiner des l’électrodes de formes plus compliquées que si elles étaient en cuivre électrolytique.
Les cupro tungstènes
Pseudo-alliages à structure parfaitement isotrope sont composés de poudre de tungstène (50 à 60 %) et de cuivre (20 à 50 %). Un alliage à haute teneur en tungstène sera plus difficile à usiner qu’un alliage à bas pourcentage. En revanche, son comportement en électroérosion sera meilleur du point de vue de l’usure, mais légèrement moins en vitesse d’usinage. Ils sont utilisés pour tous les usinages de pièces de carbure de tungstène, pour les usinages d’orifices traversant une pièce de part et d’autre très profond, pour les usinages de précision avec des détails très fins et répétitifs.
Les graphites
Le graphite est devenu le matériau plus utilisé en électro érosion pour la confection des électrodes. Il en existe une très variété sur le marché dont le comportement en électro érosion est directement lié à la densité et à la grosseur des grains.
Le graphite de faible densité (1.6 à 1.7) permettra des enlèvements de matières plus importante que le graphite dense (1.8 à 1.85). Cependant, les taux d’usure volumétrique et plus spécialement la tenue des angles sont meilleurs sur ce dernier.
La finesse des grains qui constituent le graphite a une influence sur l’état de surface de l’électrode, de même que sur l’état de la surface usinée. Ainsi, un graphite à grains fins autorise l’obtention d’électrodes dont l’état de surface est excellent et qui, lors de l’usinage de finition, permettra d’obtenir un meilleur état de surface qu’avec un graphite à gros grains. De plus, la résistance à l’effritement des anges est améliorée.
Les aciers
Tous ls aciers à outils peuvent très bien être utilisés comme matériaux d’électrode. Cependant, les rendements sont nettement moins bons que ceux obtenus avec le cuivre (enlèvement de matière inférieur de 50 à 60 % et usure supérieur de 50 à 100 %). L’application la plus importante d’électro érosion acier sur acier est celle qui consiste à usiner les plans de joint pour la fermeture des moules pou l’injection de matières plastiques et les formes d’outils d’emboutissage pour garantir un jeu constant entre les deux parties.
Régimes d’usinage
Chaque décharge engendre un cratère, c’est-à-dire une alvéole creusée dans la pièce usinée ayant la forme d’une calotte sphérique. Son volume est directement fonction du temps d’impulsion de décharge et de son intensité : le régime d’usinage choisi.
Dans la grande majorité des applications, il n’est pas conseillé d’utiliser un seul régime d’usinage correspondant à l’état de surface désiré. On a tout avantage, pour diminuer les temps d’usinage, à choisir des régimes d’ébauche, de semi-finition et finition, même si cela nécessite l’utilisation de plusieurs électrodes avec des sous-dimensionnements différents (le sous-dimensionnement d’une électrode correspond au gap pour le régime de finition et au gap additionné de la rugosité de la zone affectée et de la sécurité de recouvrement pour les autres régimes.).
En règle générale, on programmera deux ou trois régimes d’usinage sur les machines d’enfonçage classiques, soit : un régime d’ébauche, un régime de finition et un régime de semi-finition.
Un régime d’ébauche est fonction de la forme et de la surface à usiner.
Un régime de finition est fonction de l’état de surface final.
Un régime de semi-finition, si la précision le nécessite ou si le coût de fabrication de la troisième électrode est compensé par la réduction du temps d’usinage permis par une étape de semi-finition.
En revanche, sur certaines machines équipées de tête ou de table planétaire et du fait des faibles taux d’usure d’électrode, on peut réaliser un usinage avec une seule électrode en augmentant le nombre de régimes d’usinage pour réduire le temps d’électroérosion, les différences de valeurs étant compensées par un déplacement de la tête ou de la table planétaire.
Caractéristiques des surface usinées
En électroérosion, l’enlèvement de matière est provoqué principalement par un phénomène thermique. Dans une décharge, la température est de l’ordre de 8 000 à 12 000°c. L’effet de ces décharges à haute température peut exercer une influence sur la structure superficielle de la matière usinée, influence plus ou moins importante selon les différentes matières. Certaines de ces matières ne présentent aucune modification de structure.
Paramètres de réglage de base
Chaque régime d’usinage est défini par un certain nombre de paramètres de réglage de base qui sont la polarité de l’électrode, le temps d’impulsion, l’intensité du courant et la tension d’amorçage.
Polarité de l’électrode
La polarité positive est la plus couramment utilisée car elle permet d’obtenir des usures d’électrode faibles et un bonne vitesse d’usinage.
La polarité négative permet d’obtenir une grande vitesse d’usinage mais des usures d’électrodes importantes fluctuent entre 15 et 30 %.
Temps d’impulsion et intensité du courant
En régime de finition c’est l’état de surface qui détermine le temps d’impulsion et l’intensité de courant.
Le régime d’ébauche est le régime de base choisi. Il permet les plus grandes vitesses d’usinage au niveau de l’intensité de courant, compte tenu de la surface frontale maximale de la cavité.
Tension d’amorçage
Ce paramètre est fonction des matériaux de l’électrode et de la pièce.
Arrosage
L’arrosage, c’est-à-dire la circulation du diélectrique entre l’électrode et la pièce usinée, est très important.
Dans le cas d’usinage sans arrosage, au début, le diélectrique est propre, c’est-à-dire exempt de particules érodées et de résidus carbonés résultants du cracking du diélectrique ; la résistance d’un diélectrique propre étant plus grande que celle d’un diélectrique chargé de particules, un délai est nécessaire pour rompre cette résistance et permettre à la première décharge de s’amorcer.
Les particules créées par les premières décharges agissent comme relais, réduisant la résistance du diélectrique, permettant ainsi aux décharges de se développer plus facilement : les conditions d’usinage sont donc améliorées.
Cependant, si la densité des particules devient trop importante dans certaines zones d’usinage, cela facilite la formation de décharges anormales qui peuvent dégénérer en arcs électriques endommageant la pièce et l’électrode. Cet excès de particules doit être éliminé par l’arrosage.
L’arrosage est donc aussi important en électroérosion que les paramètres électriques de réglage. Il ne doit être ni trop puissant ni trop faible, le meilleur rendement étant obtenu avec un faible taux de contamination du diélectrique.
Les modes d’arrosages
Différents modes d’arrosage peuvent être utilisés selon les problèmes à traiter. Chez Micro Érosion, nous utilisons un seul mode d’arrosage : l’arrosage par brassage. Ce mode d’arrosage est obtenu au moyen du mouvement de pulsation de l’électrode : lorsque l’électrode se retire, le volume du gap augmente, ce qui a pour effet d’amener du liquide propre qui se mélange au liquide chargé de particules. Lorsque ensuite l’électrode descend, les particules sont évacuées. Ce brassage se fait à rythme régulier (toutes les 5 à 10 secondes). Ce mode est intéressant, car il permet l’usinage d’orifices très profonds sans circulation forcée du liquide diélectrique. Il en existe cependant d’autres :
Arrosage par injection : dans ce mode d’arrosage, l’injection du liquide diélectrique sous pression s’effectue soit à travers la pièce soit à travers l’électrode.
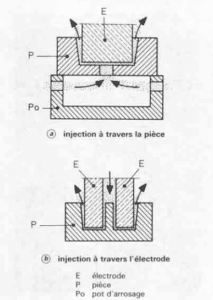
Arrosage par jet latéral : ce mode d’arrosage doit être utilisé seulement s’il n’est pas possible de prévoir soit dans la pièce, soit dans l’électrode, un ou plusieurs orifices d’arrosage. Ces cas se présentent, par exemple, lors de l’usinage de matrices de médailles, de couverts ou l’usinage de fentes étroites dans les moules en plastique. La réalisation de ce type d’arrosage nécessite l’utilisation de buses ou de rampes d’injection dont l’orientation doit être soigneusement étudiée pour assurer le lavage de toute la zone de travail.
Arrosage par aspiration : le liquide est aspiré soit à travers la pièce soit à travers l’électrode. Comparée à l’arrosage par injection, cette technique permet d’éviter l’électroérosion latérale parasite en supprimant la circulation des particules le long des parois verticales : l’orifice ainsi obtenu est pratiquement cylindrique. Ce type d’arrosage est limité aux petites pièces, les machines utilisées ayant généralement une capacité de dépression limitée à quelques bars.
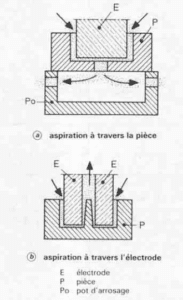
Arrosage pulsé synchronisé avec le relevage de l’électrode : ce mode d’arrosage est utilisé dans le cas d’usinage avec une électrode métallique (cuivre ou cuprotungstène) ; une usure anormale se présente alors autour des trous d’injection. Pour éliminer ce désagrément, on peut injecter le liquide pendant le temps durant lequel l’électrode remonte, donc lorsqu’il n’y a pas d’usinage. Pour cela, il est nécessaire de raccorder l’électrode à la sortie, injection pulsée, de la machine.